Comprehensive Overview: What is Porosity in Welding and Just How to stop It
Comprehensive Overview: What is Porosity in Welding and Just How to stop It
Blog Article
The Science Behind Porosity: A Comprehensive Overview for Welders and Fabricators
Understanding the intricate mechanisms behind porosity in welding is essential for welders and fabricators striving for impressive craftsmanship. As metalworkers dig right into the midsts of this sensation, they uncover a world regulated by numerous elements that affect the development of these minuscule spaces within welds. From the composition of the base products to the ins and outs of the welding process itself, a plethora of variables conspire to either worsen or ease the existence of porosity. In this comprehensive overview, we will certainly unwind the science behind porosity, discovering its impacts on weld high quality and unveiling progressed strategies for its control. Join us on this trip via the microcosm of welding blemishes, where precision meets understanding in the quest of remarkable welds.
Understanding Porosity in Welding
FIRST SENTENCE:
Assessment of porosity in welding discloses critical insights right into the stability and high quality of the weld joint. Porosity, characterized by the visibility of tooth cavities or voids within the weld metal, is a common worry in welding procedures. These gaps, if not properly attended to, can endanger the structural honesty and mechanical residential or commercial properties of the weld, bring about potential failings in the ended up item.

To detect and evaluate porosity, non-destructive testing methods such as ultrasonic screening or X-ray assessment are frequently used. These methods enable the recognition of inner problems without jeopardizing the honesty of the weld. By evaluating the dimension, form, and distribution of porosity within a weld, welders can make informed decisions to enhance their welding processes and attain sounder weld joints.

Variables Influencing Porosity Development
The event of porosity in welding is affected by a myriad of aspects, varying from gas securing efficiency to the complexities of welding specification setups. Welding parameters, including voltage, existing, take a trip speed, and electrode type, also impact porosity development. The welding strategy utilized, such as gas metal arc welding (GMAW) or protected metal arc welding (SMAW), can influence porosity development due to variations in heat distribution and gas coverage - What is Porosity.
Results of Porosity on Weld Top Quality
Porosity development considerably compromises the structural honesty and mechanical properties of bonded joints. When porosity exists in a weld, it creates spaces or dental caries within the material, reducing the general strength of the joint. These spaces click here to read work as stress and anxiety concentration factors, making the weld much more vulnerable to cracking and failing under load. The visibility of porosity additionally weakens the weld's resistance to deterioration, as the entraped air or gases within the spaces can respond with the surrounding environment, bring about destruction with time. Additionally, porosity can hinder the weld's ability to endure stress or impact, further jeopardizing the overall high quality and integrity of the welded framework. In important applications such as aerospace, vehicle, or architectural building and constructions, where security and toughness are extremely important, the harmful effects of porosity on weld high quality can have severe repercussions, highlighting the importance of minimizing porosity through appropriate welding methods and procedures.
Strategies to Lessen Porosity
In addition, using the appropriate welding criteria, such as the proper voltage, existing, and take a trip rate, is crucial in avoiding porosity. Keeping a consistent arc size and angle throughout welding additionally aids Visit Your URL minimize the likelihood of porosity.

Making use of the ideal welding technique, such as back-stepping or employing a weaving movement, can also help distribute heat evenly and decrease the opportunities of porosity formation. By implementing these techniques, welders can effectively lessen porosity and create high-grade welded joints.
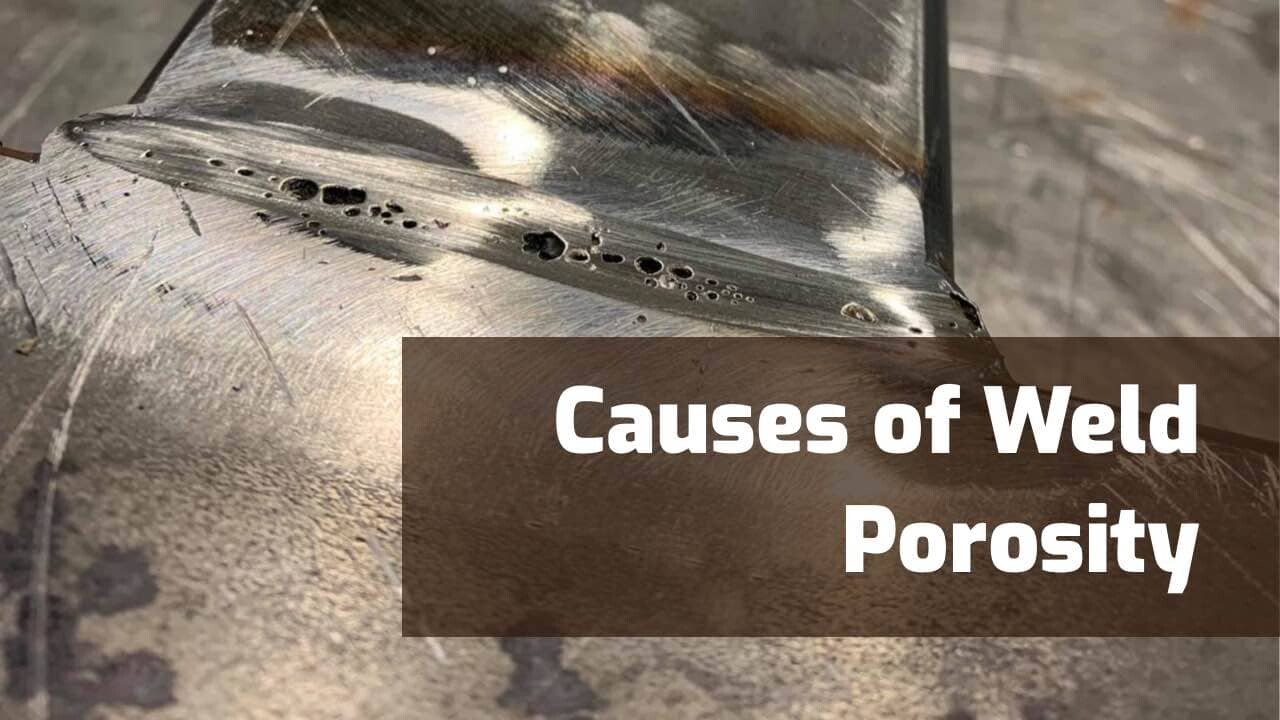
Advanced Solutions for Porosity Control
Implementing advanced technologies and innovative techniques plays a critical duty in accomplishing exceptional control over porosity in welding processes. In addition, employing innovative welding techniques such as pulsed MIG welding or modified atmosphere welding can also help reduce porosity problems.
One more sophisticated service involves the use of innovative welding devices. For example, using devices with built-in features like waveform control and sophisticated source of power can This Site improve weld quality and minimize porosity risks. The execution of automated welding systems with exact control over criteria can substantially reduce porosity issues.
Moreover, integrating sophisticated monitoring and examination technologies such as real-time X-ray imaging or automated ultrasonic screening can help in detecting porosity early in the welding procedure, permitting for instant corrective actions. In general, integrating these sophisticated options can substantially enhance porosity control and boost the overall quality of welded elements.
Final Thought
To conclude, recognizing the scientific research behind porosity in welding is essential for welders and makers to create premium welds. By identifying the factors influencing porosity formation and carrying out methods to minimize it, welders can improve the general weld top quality. Advanced solutions for porosity control can additionally improve the welding process and make sure a solid and reputable weld. It is necessary for welders to continuously educate themselves on porosity and execute ideal methods to achieve optimum outcomes.
Report this page